Introducing the concept prototype of a portable stabilizer for extreme filming, ingeniously crafted long before DJI even entered the game.
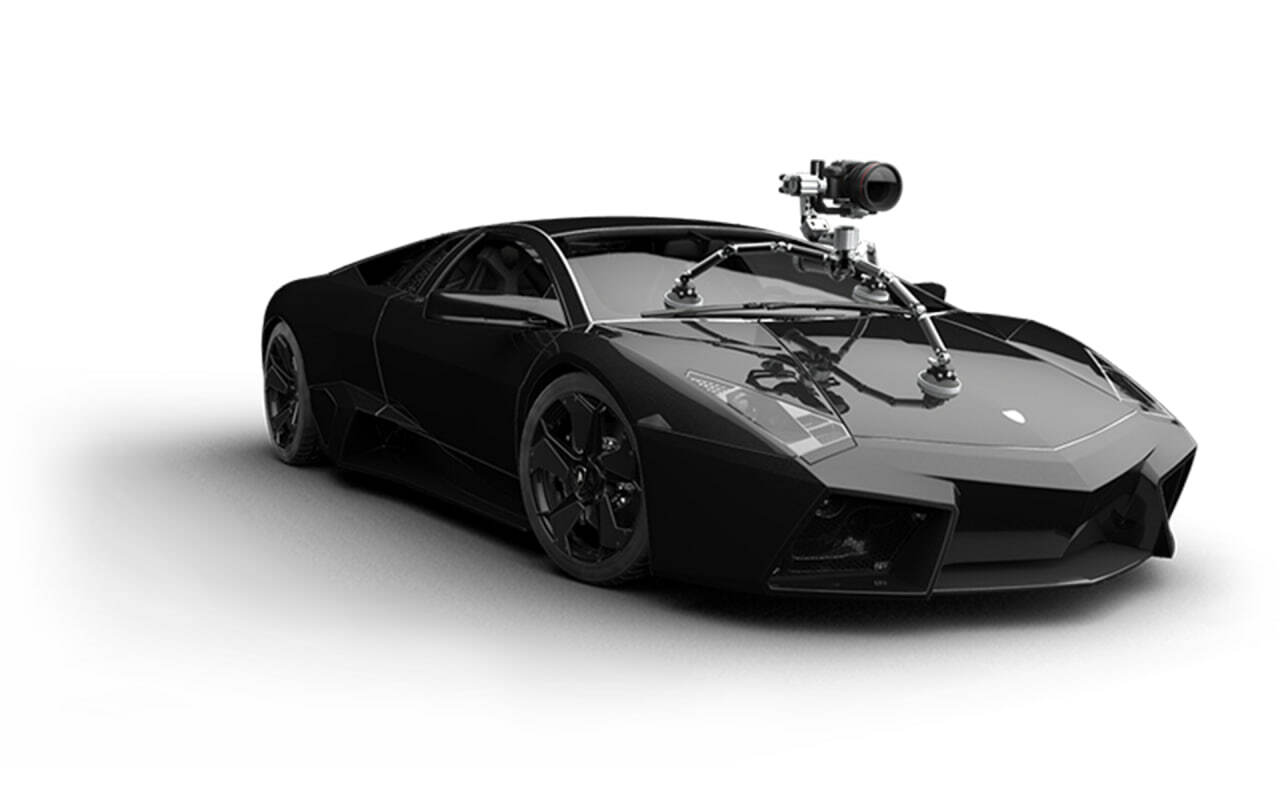
The Story
In 2015, following the wrap-up of the "Hardcore Henry" film's shooting period, I traveled to the island of Koh Phangan. There, I took the time to rejuvenate, train, and refine my cinematography skills, experimenting with the then-novel three-axis electronic brushless stabilizers for cameras.
At the time, the market was enthusiast-driven. DJI stabilizers were non-existent, and ready-to-use Plug and Play solutions were simply not available. A camera stabilizer purchase meant receiving a kit of aluminum parts from China that required advanced electronic know-how to set up and calibrate the motors for acceptable camera stabilization. This is what I devoted my free time to mastering...
In my experiments with controller boards, I discovered that the most stable and popular controller, supplied in all Chinese devices, was a product of the Russian startup BASECAM. I also connected with engineers from another Russian startup, Research Creators Park, who had built a carbon stabilizer prototype named K-Gimbal. This was far more reminiscent of a functional product than the Chinese crafts.
I reached out to the company and became their ambassador for several years, constantly providing feedback to the developers and introducing several improvements that, at that time, simply hadn't occurred to anyone because the engineers lacked the necessary operational experience.
At the time, the market was enthusiast-driven. DJI stabilizers were non-existent, and ready-to-use Plug and Play solutions were simply not available. A camera stabilizer purchase meant receiving a kit of aluminum parts from China that required advanced electronic know-how to set up and calibrate the motors for acceptable camera stabilization. This is what I devoted my free time to mastering...
In my experiments with controller boards, I discovered that the most stable and popular controller, supplied in all Chinese devices, was a product of the Russian startup BASECAM. I also connected with engineers from another Russian startup, Research Creators Park, who had built a carbon stabilizer prototype named K-Gimbal. This was far more reminiscent of a functional product than the Chinese crafts.
I reached out to the company and became their ambassador for several years, constantly providing feedback to the developers and introducing several improvements that, at that time, simply hadn't occurred to anyone because the engineers lacked the necessary operational experience.
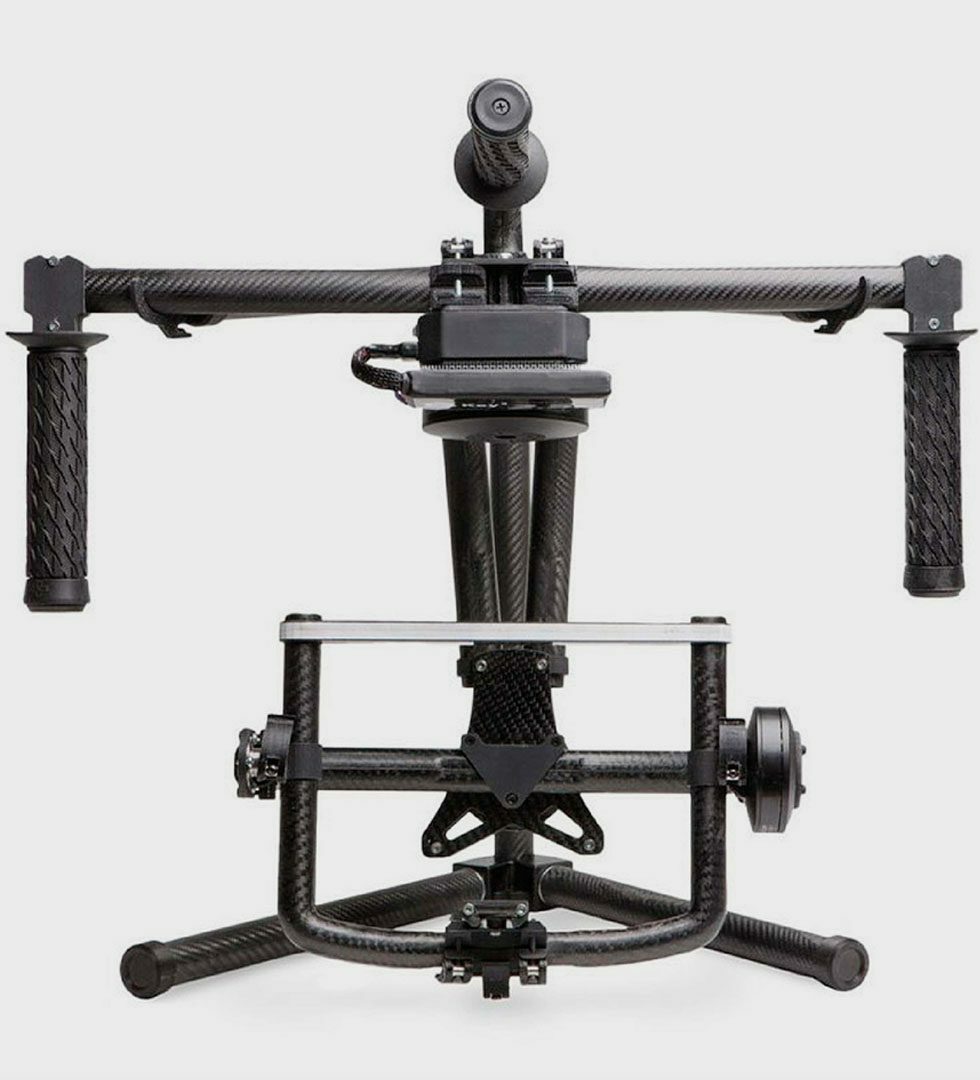
On their fully modified stabilizer, I shot the majority of the footage for my very first directorial and cinematographic action showreel.
The first improvements I implemented significantly transformed the device's ergonomics:
Firstly, I inverted the stabilizer to position the camera on top, allowing for direct monitor viewing without the need for additional displays. This streamlined the setup, enabling longer shooting sessions without fatigue.
Back then, even such a basic procedure as "inverted" mode shooting, which now seems like common sense and is widely used by all manufacturers, was akin to discovering America.
I had to write a custom profile for the controller board and manually calibrate all the parameters to achieve satisfactory results. And it worked...
Back then, even such a basic procedure as "inverted" mode shooting, which now seems like common sense and is widely used by all manufacturers, was akin to discovering America.
I had to write a custom profile for the controller board and manually calibrate all the parameters to achieve satisfactory results. And it worked...
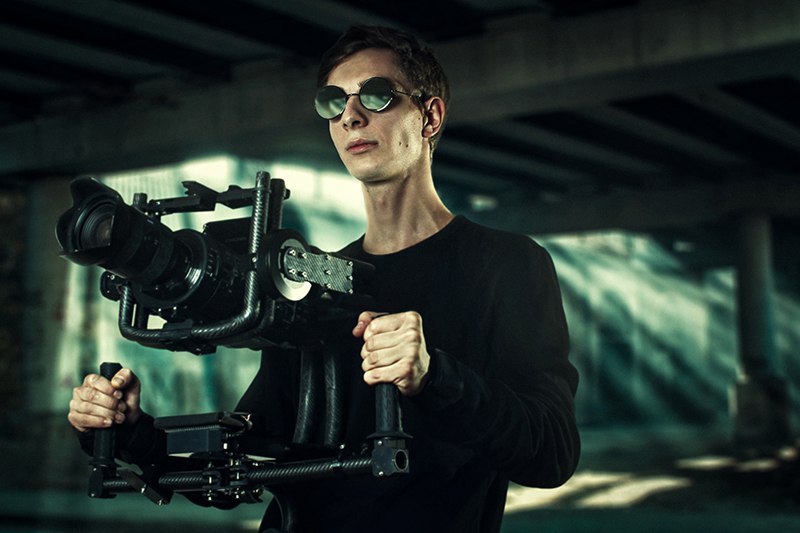
Next, I moved the stabilizer's handles closer together to reduce strain and allow for a more even weight distribution. Following my request, the engineers crafted a mount that enabled the attachment of a monopod to the stabilizer, effectively turning it into a portable "crane."
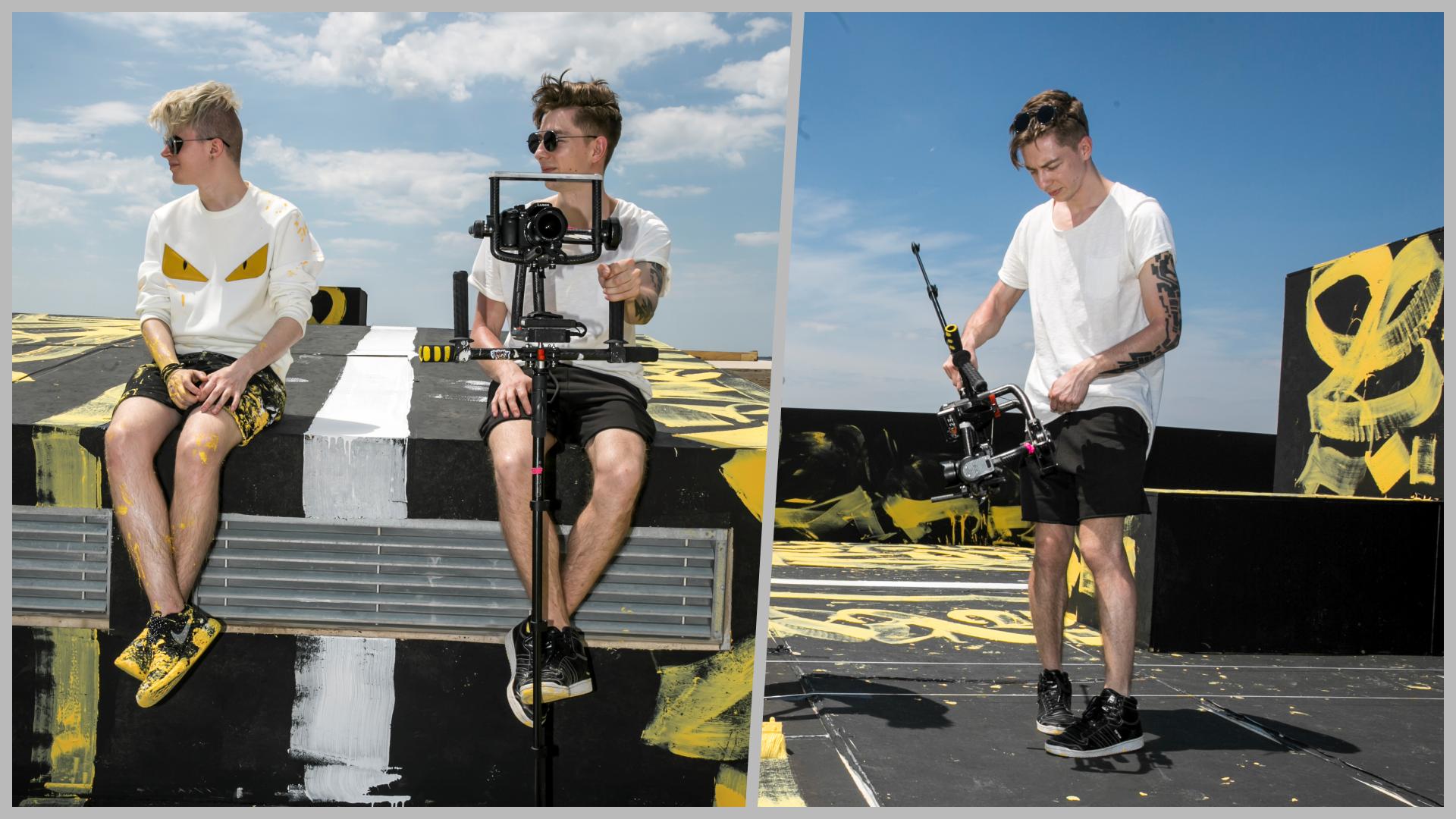
Looking ahead, I can say that these ideas were in the zeitgeist, and within a few years, DJI and other major stabilizer manufacturers had made all these concepts industry standards.
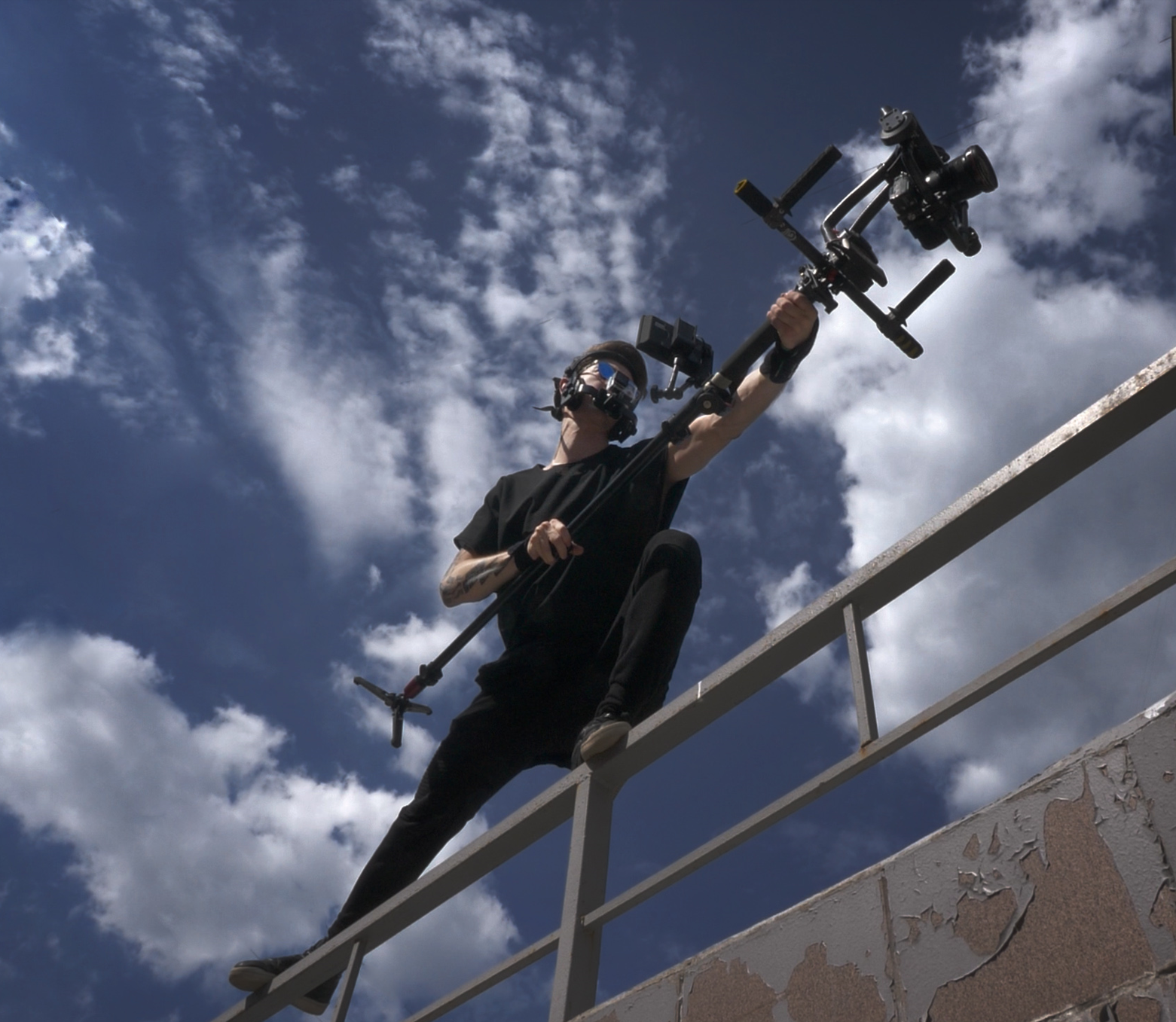
As I honed my craft, I realized that although my modified stabilizer had become a superb tool, it was still too bulky and required a serious ergonomic redesign. Thus, I began constructing "training" stabilizers from water bottles and bamboo, allowing me to perform stunts without risking expensive cameras and to experiment with proper weight balancing. This inspired the idea of building a new stabilizer from scratch, tailored to my needs.
The more I practiced, the clearer the vision of the final product became in my mind. This inspired me to negotiate with Research Creators Park to initiate a project for a stabilizer that I named the Action Gimbal.
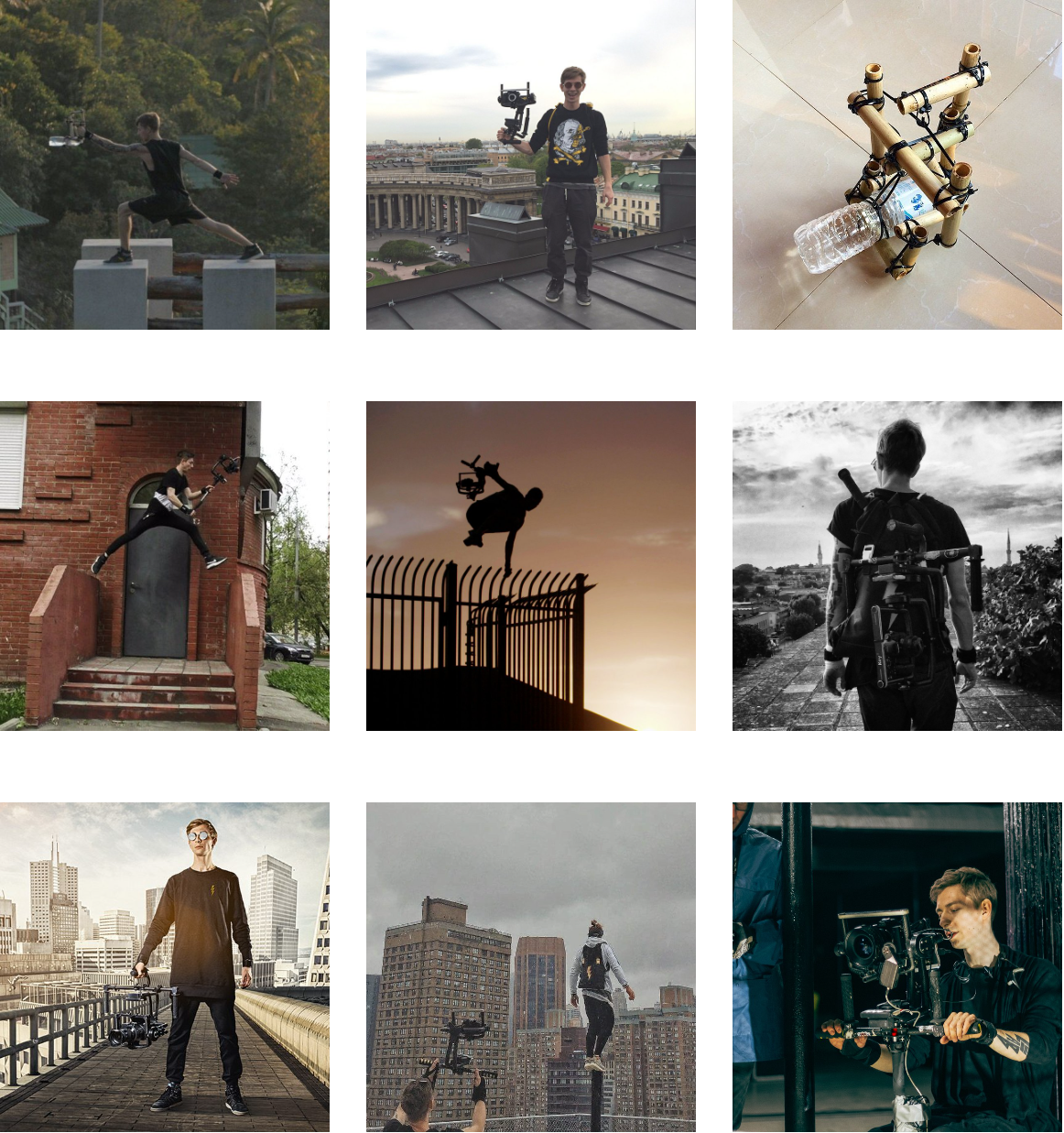
I funded the development and served as the concept designer, while Arseniy Sentyakov handled all the engineering aspects of the device.
DESIGN
2016-2017
My concept aimed to significantly reduce and lighten the frame of the device, making it portable enough to fit in a lady's purse, yet powerful enough to support the weight of a portable Mirrorless camera.
The primary grip of the stabilizer was to be the inverted "mode".
Additionally, I suggested designing the handle in such a way that the battery could be swapped out like a magazine in a pistol.
I also integrated a joystick into the handle for added convenience.
The primary grip of the stabilizer was to be the inverted "mode".
Additionally, I suggested designing the handle in such a way that the battery could be swapped out like a magazine in a pistol.
I also integrated a joystick into the handle for added convenience.
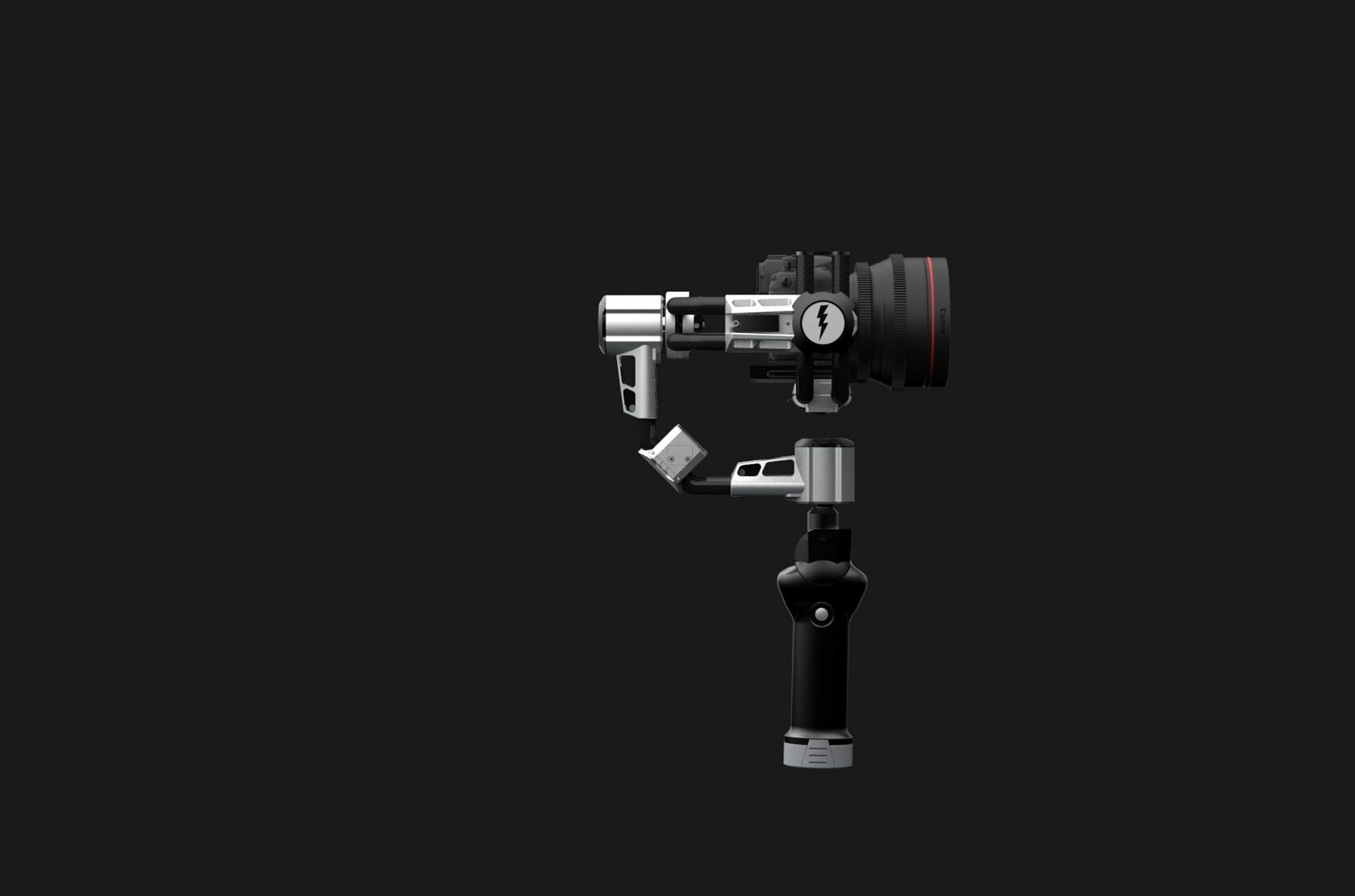
Additionally, I conceived the idea of portable handle modules that could be docked to the base of the device, offering broad possibilities for modifying the grip's position.
From these handles, one could assemble, for instance, a shoulder rig that would allow for better weight distribution.
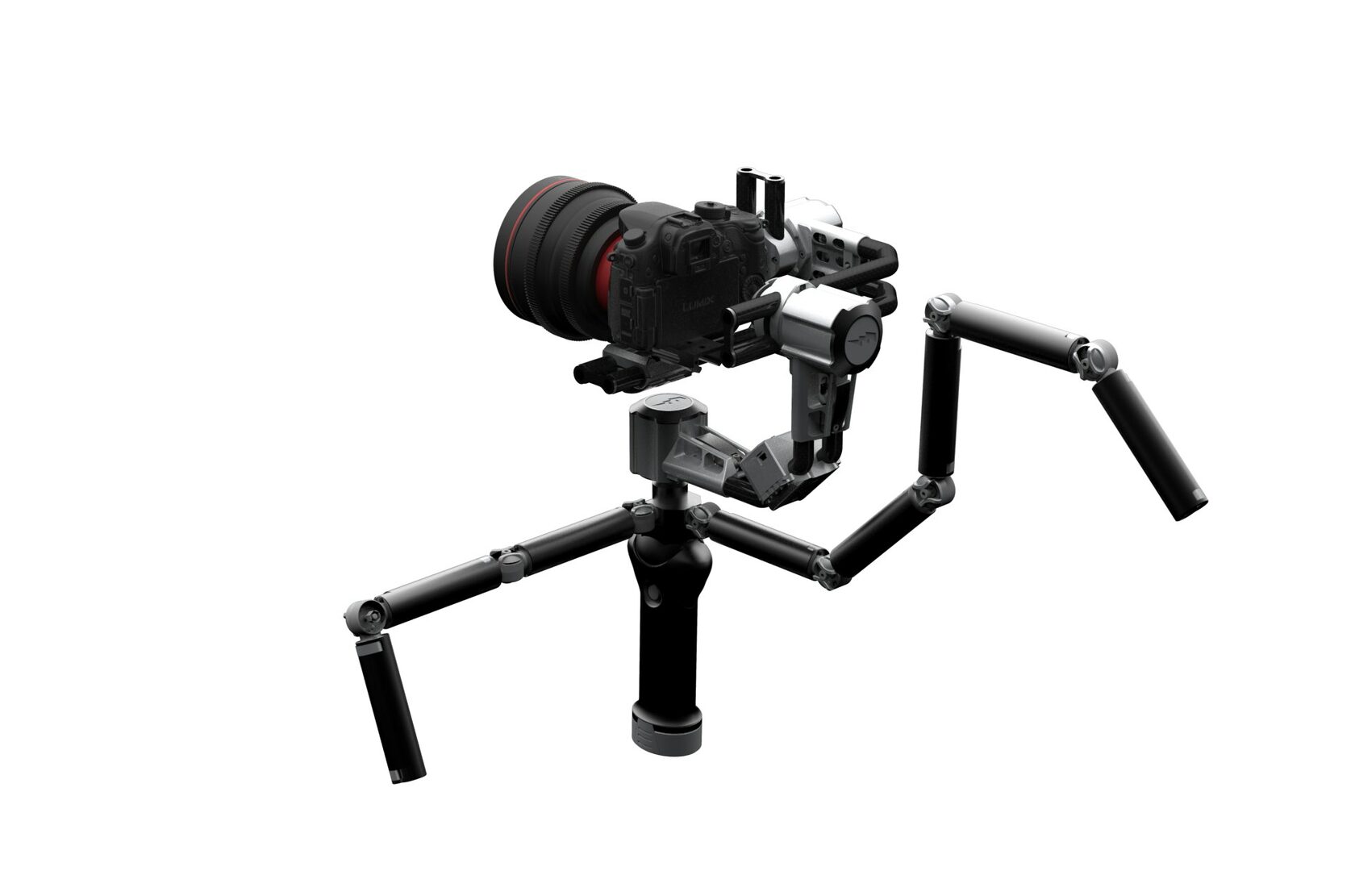
These portable handles were intended to be sold separately, allowing operators to independently decide which configurations are convenient for them to solve specific tasks.
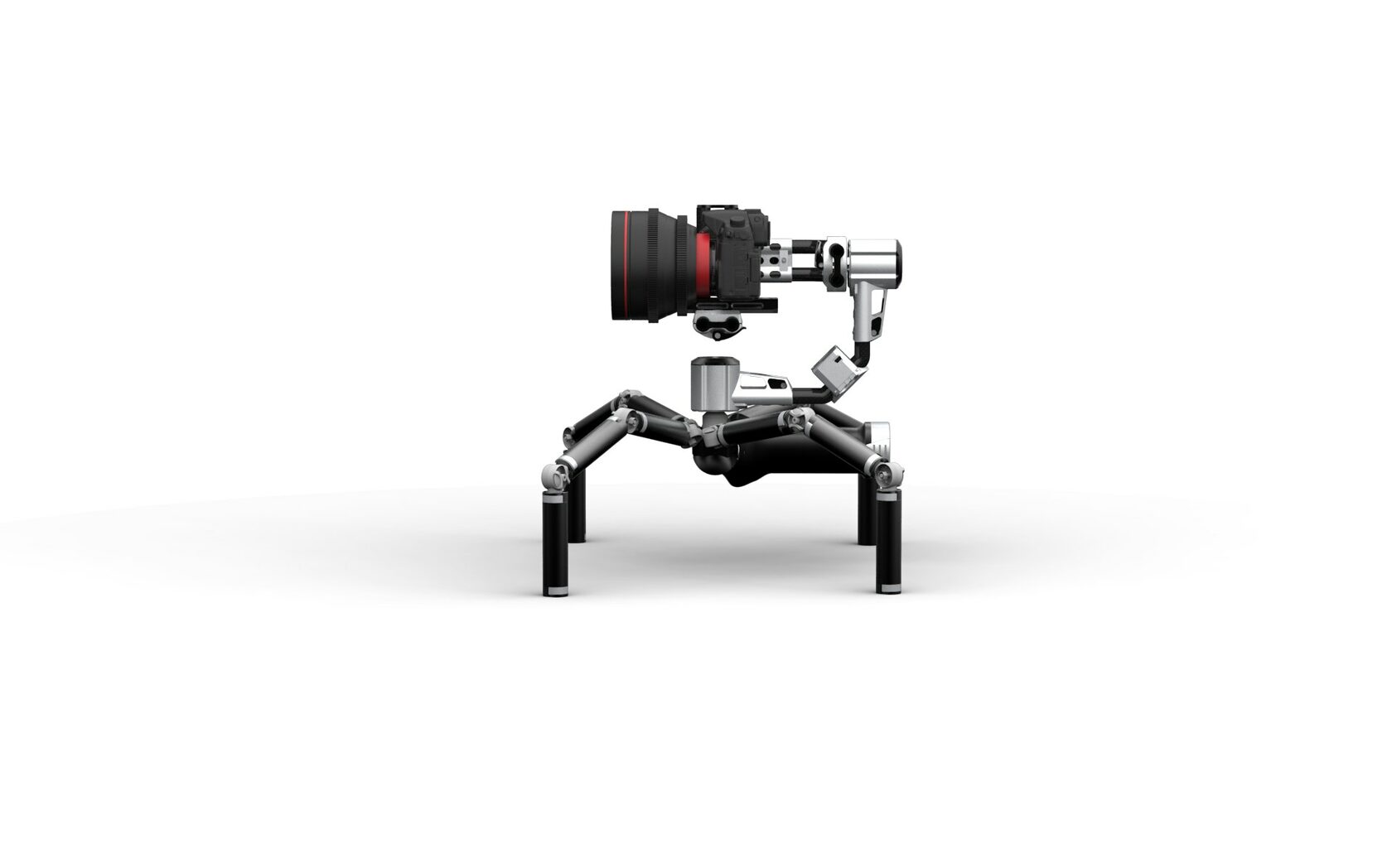
The main handle of the stabilizer featured a special joint that allowed for a wide range of grips during filming.
Ergonomics has always been important to me as a camera operator, so I sought out and designed versatile solutions suitable for even non-standard situations.
Ergonomics has always been important to me as a camera operator, so I sought out and designed versatile solutions suitable for even non-standard situations.
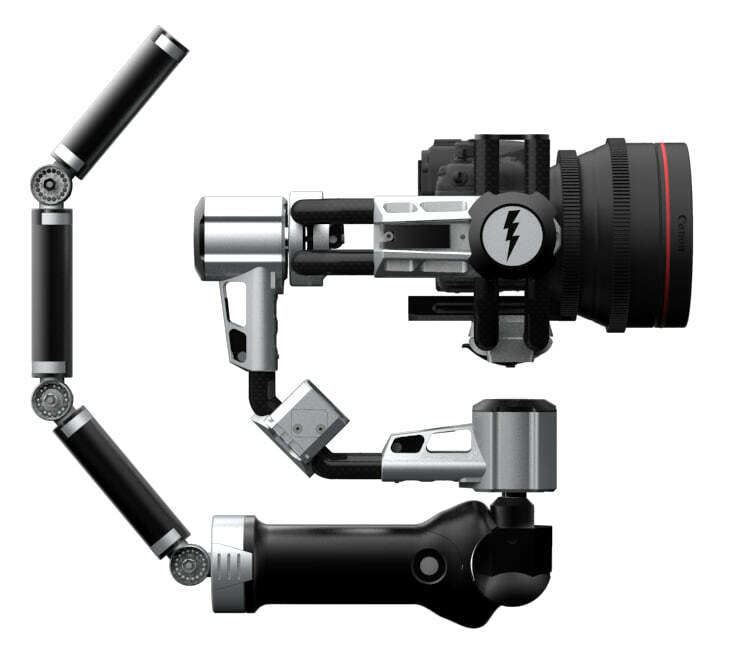
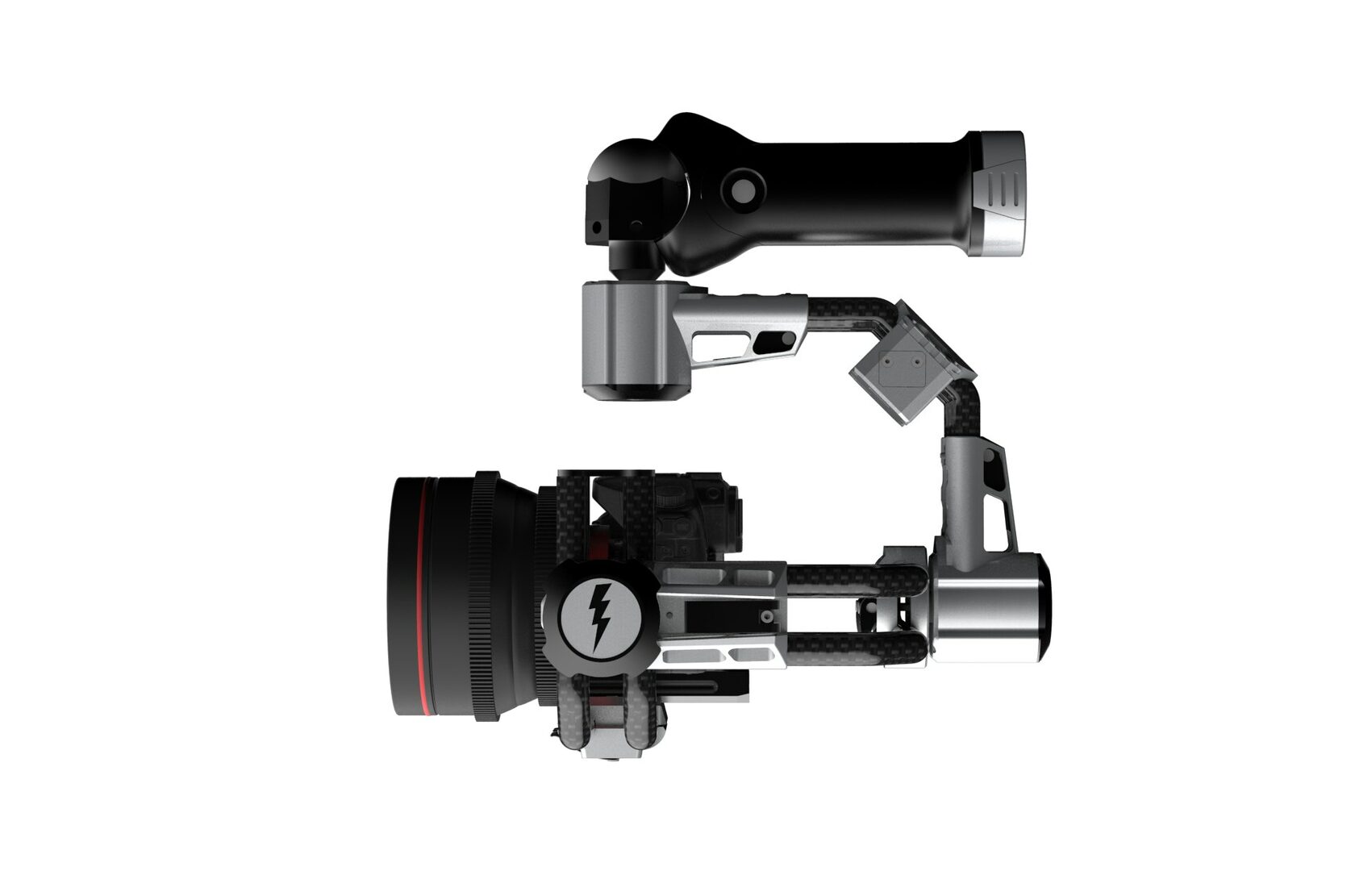
The entire frame of the stabilizer was constructed from carbon fiber tubes and aluminum, in order to minimize weight while remaining an extremely strong and monolithic structure!
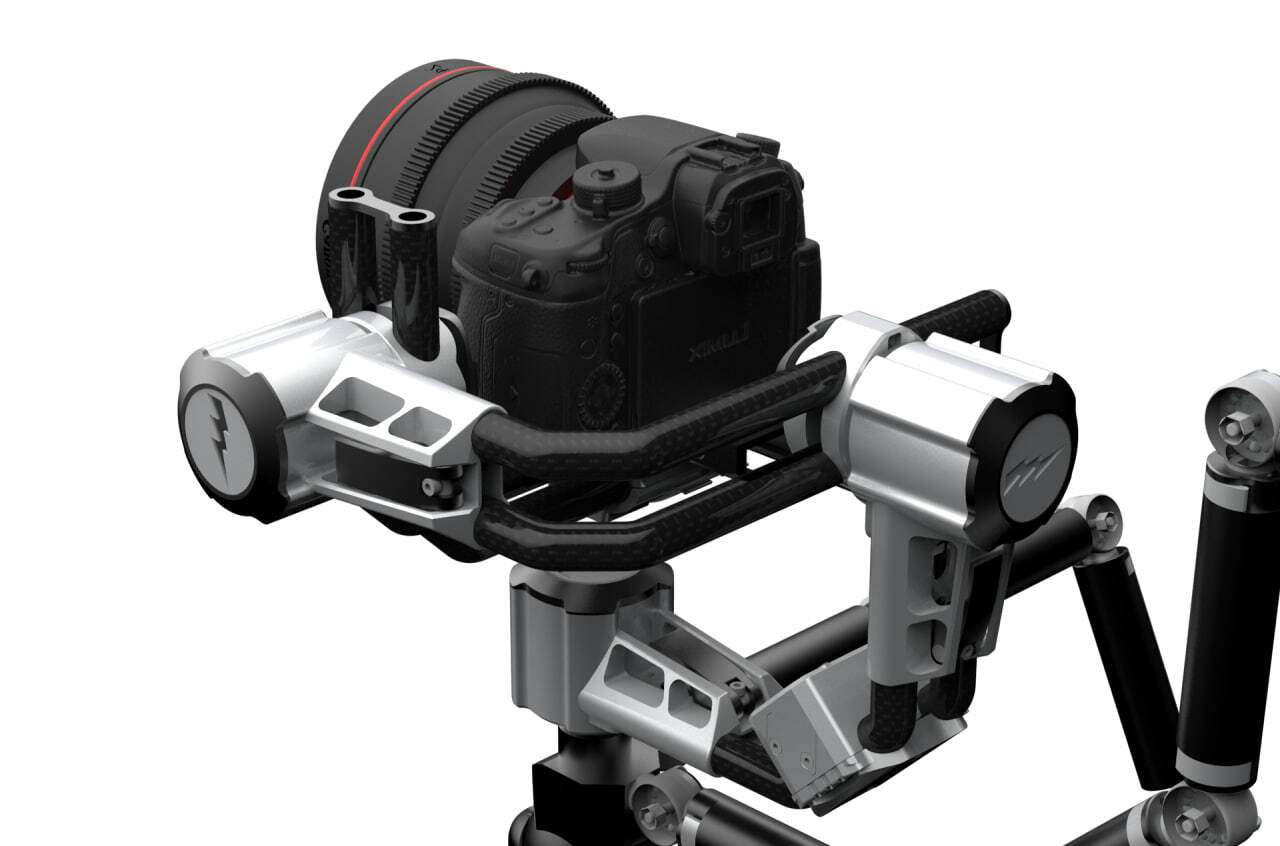
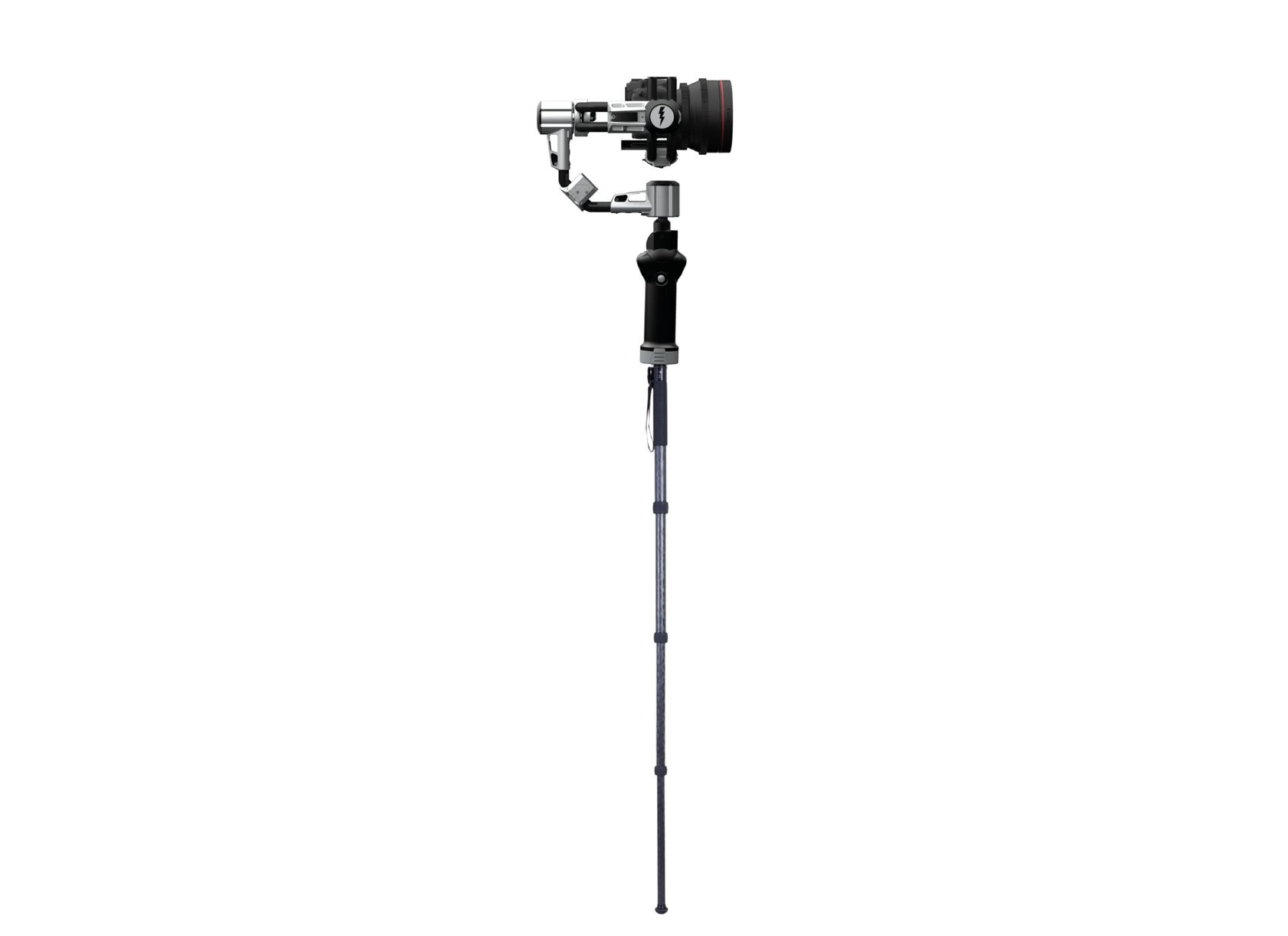
The additional handle mounts were designed to be compatible with car suction cups, clamps, and various grips, allowing the stabilizer to be securely attached to virtually any surface.
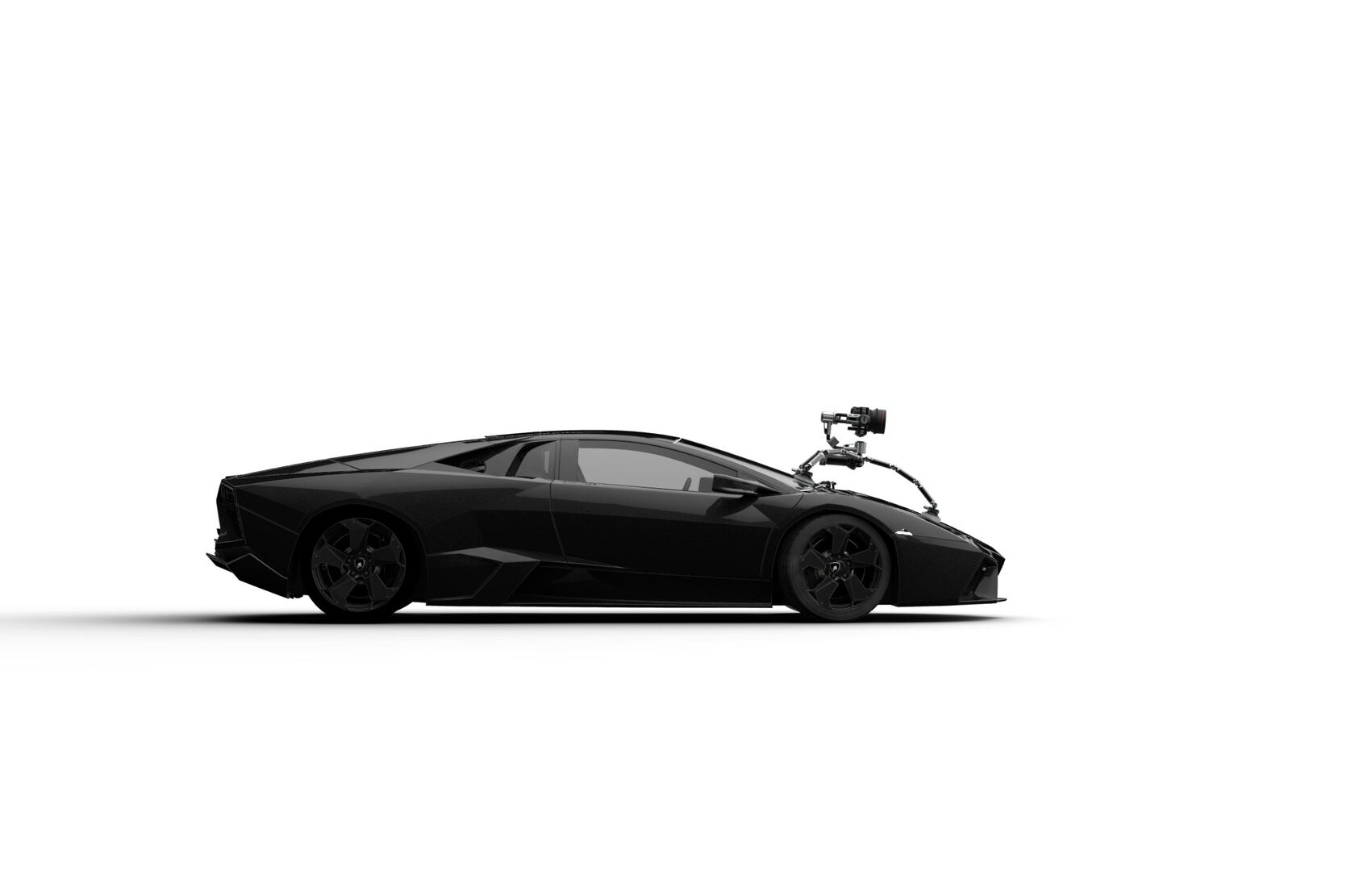
We built two prototypes of the device. The first was made from 3D-printed plastic, while the second was crafted from aluminum.
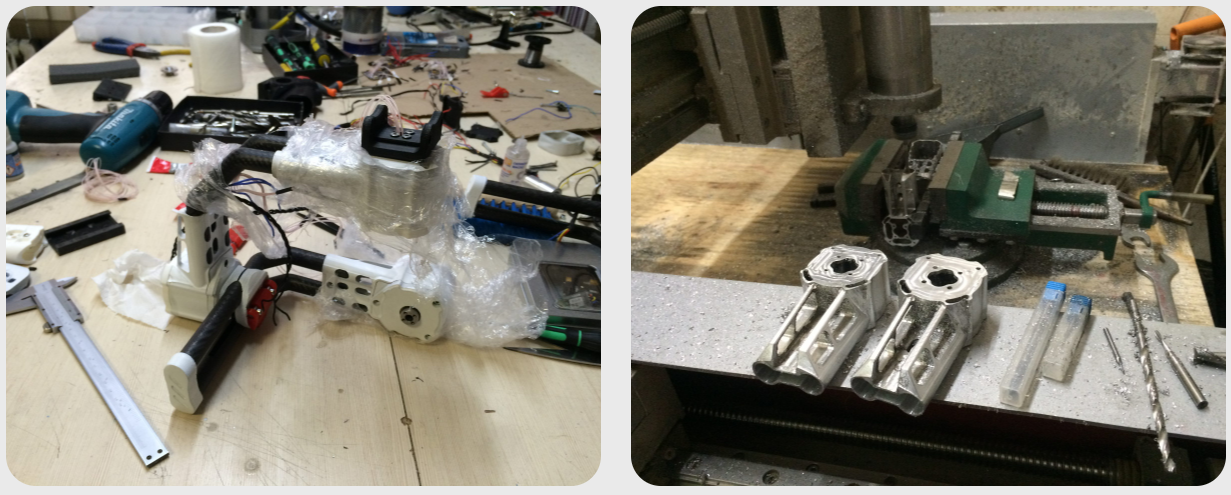
Unfortunately, our technological capabilities didn't allow us to manufacture some parts with the necessary degree of high precision as can be done in full-scale factories. Therefore, a significant amount of defective products occurred during the process, which prevented us from turning this concept into a full-fledged mass production.
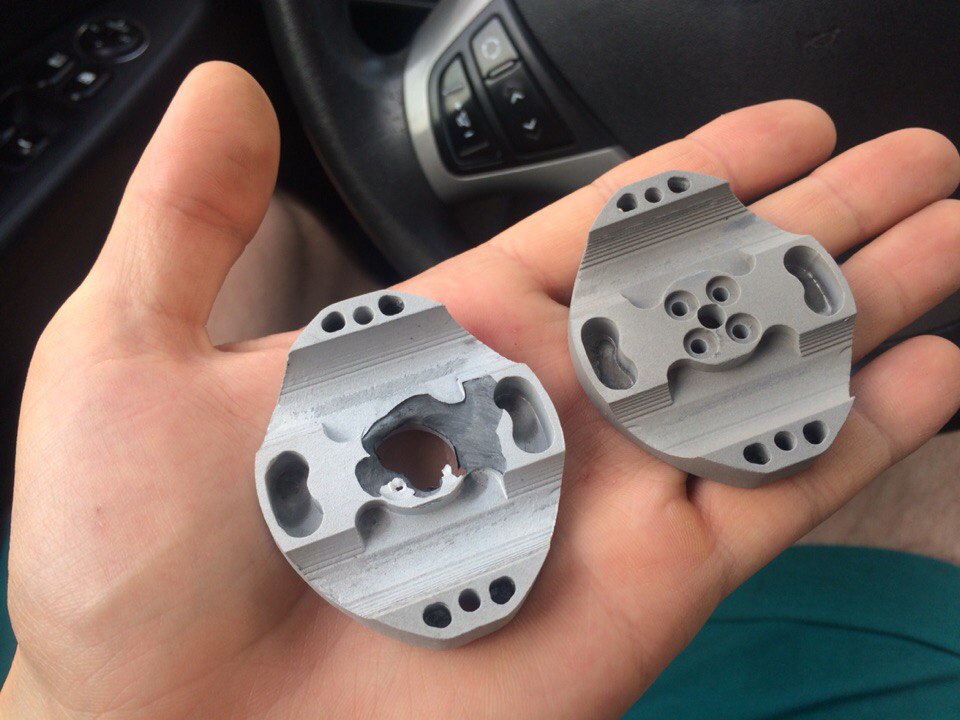
Nevertheless, the functioning prototype became my personal operating tool, which is now stored in my own museum of ideas and prototypes.
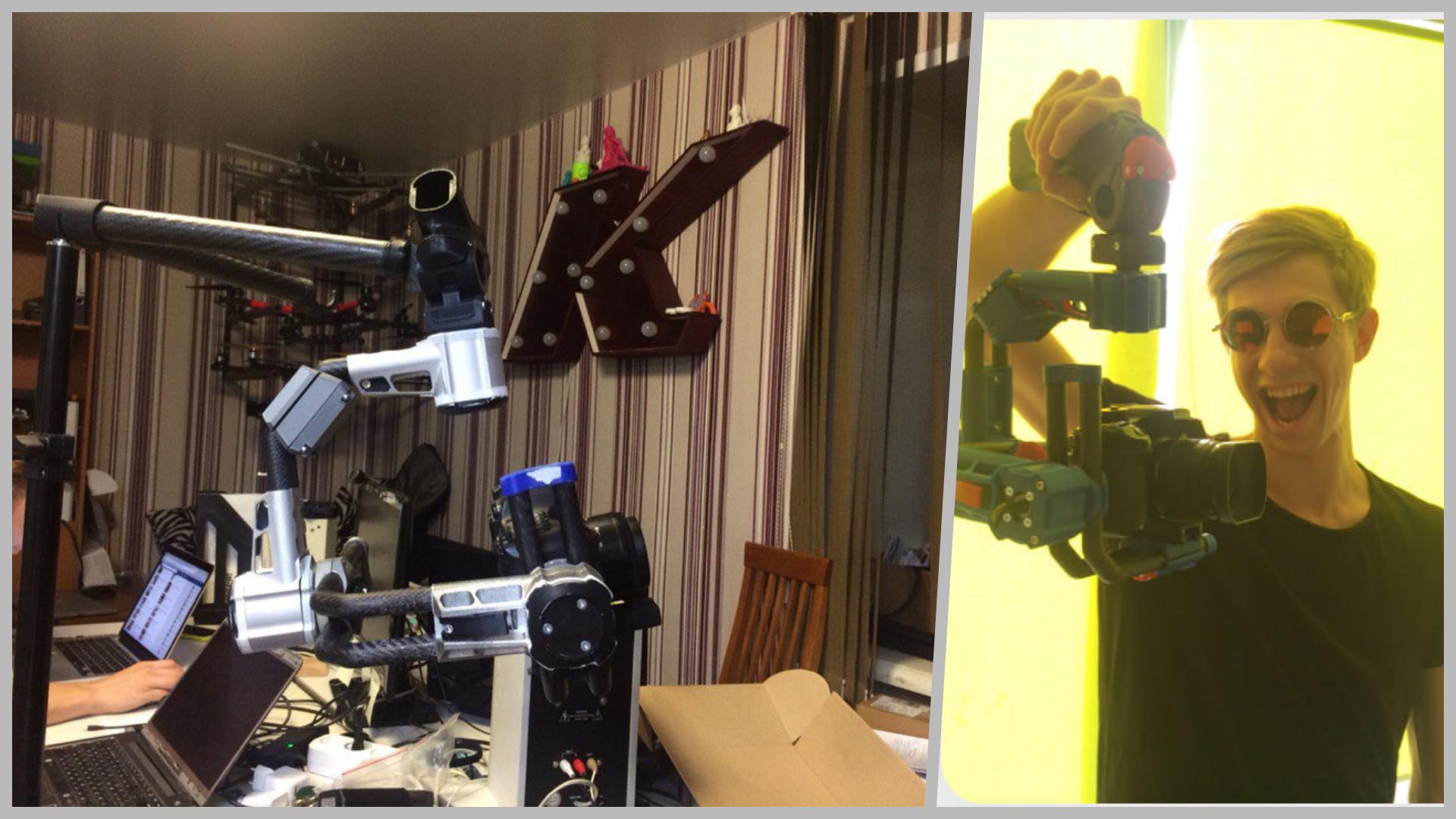
In the course of advancing my concept, I entered discussions with potential American investors to evolve the idea into a nascent startup. Alas, the venture's destiny took a different turn. DJI, a colossus in the tech arena, launched a remarkably similar device, underpinned by their expansive production scale and hefty financial backing.
Faced with such formidable competition, I recognized the impracticality of contending on an uneven playing field — the disparity in resources, resolve, and capital was clear. Hence, I made the strategic call to conclude the endeavor, maintaining the project's status as a proof-of-concept prototype. This prototype, however, served as a personal asset in my cinematographic endeavors, echoing the practical utility of the Adventure Mask.
Despite the project's pivot, the journey through stabilizer development was enriching, steeping me further into the intricacies of engineering and validating the forward-thinking nature of my concepts — often outpacing the innovation trajectory of larger corporate entities.
Faced with such formidable competition, I recognized the impracticality of contending on an uneven playing field — the disparity in resources, resolve, and capital was clear. Hence, I made the strategic call to conclude the endeavor, maintaining the project's status as a proof-of-concept prototype. This prototype, however, served as a personal asset in my cinematographic endeavors, echoing the practical utility of the Adventure Mask.
Despite the project's pivot, the journey through stabilizer development was enriching, steeping me further into the intricacies of engineering and validating the forward-thinking nature of my concepts — often outpacing the innovation trajectory of larger corporate entities.
It is gratifying to witness how these once-novel ideas have been woven into the fabric of consumer stabilizer technology, transforming the ease and efficiency of professional creative work...